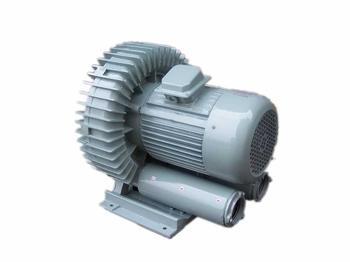
2. During the process of driving, parking or running the fan, if abnormal phenomena are found, it shall be checked immediately.
3. After the fan has been operated for the first time for one month, it should be renewed to replace the oil (fat).
Common faults The fan working medium in the cement industry often contains a certain amount of same-sized particles of different sizes and shapes, such as the induced draft fan of the dust removal system and the blower for pneumatic conveying. Because these fans work in a dust-laden air stream, the dust particles in the air stream must not only cause wear to the fan, but also deposit dust on the fan blades, and the wear and dust accumulation are not uniform. As a result, the balance of the rotor of the fan is damaged, causing vibration of the fan and shortening the life of the fan. In severe cases, the fan may not work properly. In particular, the wear of the fan blades is the most serious. It not only destroys the flow characteristics in the fan, but also easily causes major accidents such as blade breakage and flying.
The wear of the transmission parts is also a common problem for fans, including various shafts, rollers, speed reducers, motors, pumps and other bearing positions, bearing seats, keyways, and threads. The traditional welding machine processing methods can easily cause materials. Damage, resulting in component deformation or fracture, has greater limitations; brush plating and spray remachining methods often require external association, not only a long repair period, high cost, but also because of the repair material or metal material, can not be fundamentally Solve the causes of wear (metal impact resistance and poor concession); many parts can only be replaced by scrap, greatly increased production costs and spare parts inventory, so that the company's good resource advantages have been idle and wasted.
Pellet Husk Shell Fired Boiler
Pellet Husk Shell Fired Boiler Quick Details:
Steam Capacity 1 to 35 ton/hr 0.7MW-24.5MW
Fuel Applicable coal, biomass, bituminous, anthracite, rice husk, bagasse, palm kernel shell
Working pressure 0.4-2.5Mpa 4bar-25bar
Steam temperature 184℃, 194℃, 204℃, 226℃
Grate Chain grate
Structure water tube, membrane wall
Heat efficiency >83%
Fuel feeding Automatic
Application Industrial production, central heating
Wood Pellet Fired Boiler,Rice Husk Fired Boiler,Palm Shell Fired Boiler,Solid Fuel Boiler,Solid Fuel Fired Boiler
Henan Yuanda Boiler Co., Ltd. , https://www.industrialeconomi.com