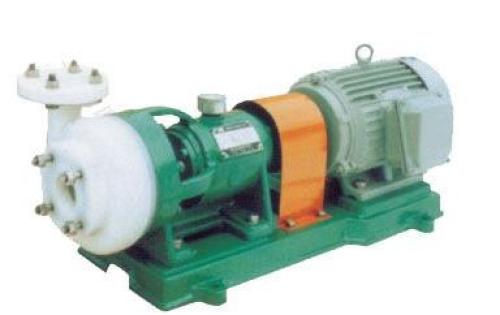
Today, energy-saving and emission-reduction are popular. How to use chemical pumps to save energy? The modern society pays attention to the concept of low-carbon environmental protection, energy conservation and emission reduction. We have also been advocating this new type of value and have put this concept into real use in our products. Reducing the leakage loss in the pump, improving the machining accuracy and assembly quality of parts, reducing the radial clearance of the throttling sleeve in front of the balancing disk and the radial clearance between the impeller front and rear sealing rings and the guide vane sealing ring, and reducing the leakage of the liquid in the pump from the high pressure side. Loss of pressure energy to the low pressure side. Today we will introduce how chemical pumps can save energy.
1 Improve the feed pump repair process to reduce hydraulic losses
During the inspection and repair, the rust, scale, burrs and flashes of the impeller and the passages of the blade passages are polished and smoothed so that the smoothness of the flow passage can reach Δ4 or more, and the frictional impact vortex loss between the water and the flow passage walls can be reduced. However, due to the limitations of on-site conditions, it is not easy to polish the entire flow section. It is important to lighten and polish the critical parts that affect the efficiency, such as the positive guide vane, the inlet of the impeller, and the exit of the impeller. Wait. Polished to see the metallic luster, must not damage the original profile of the runner. Improve the smoothness of the outer wall of the impeller and the inner wall of the pump shell. During the overhaul, the embroidered dirt and burrs on the outer wall of the impeller and the inner wall of the pump shell are polished smooth, while keeping the scoop of the impeller not exceeding the specified value and reducing friction loss of the disc.
2 reduce volume loss and improve operating efficiency
Reducing the leakage loss in the pump, improving the machining accuracy and assembly quality of parts, reducing the radial clearance of the throttling sleeve in front of the balancing disk and the radial clearance between the impeller front and rear sealing rings and the guide vane sealing ring, and reducing the leakage of the liquid in the pump from the high pressure side. Loss of pressure energy to the low pressure side. For parts such as the impeller seal ring, the guide vane sleeve, and the balance throttling disk, the materials with higher hardness should be used, and the heat treatment for improving the wear resistance should be performed. When starting the feed pump in cold state, the pump should be fully heated according to the regulations. If the heat pump is not sufficient, the upper and lower parts of the pump body will easily generate a large thermal temperature difference, which will cause the rotor to bow and deform. At this time, the internal seal gap is easily enlarged by starting the pump. Internal leakage and increased return volume loss.
3Reduce the leakage loss of the water supply system
Under normal operating conditions, the water discharge gates, trapdoors and pump body discharge gates of the water supply system, the regular sewage discharge gates of the boilers, and the accident discharge gates shall be closed tightly. After the hand touches the inspection doors, it shall be cool. Lax valves should be handled in time. Reduce the leakage loss of the feed pump recirculation door. The feed water pump recirculation device is used to keep the feed water pump started, just put into operation, and maintain a minimum flow when the boiler water supply is stopped, so as to prevent the flow due to small flow and heat, vaporization of water supply, and accidents. The recirculation door should be closed tightly during normal operation. At the site, due to structural and material problems, the recirculation door is exposed to a large pressure differential and the leakage is generally severe. A large amount of high-pressure feedwater returns to the deaerator for useless work, resulting in wasted electrical energy and even affecting boiler feedwater. At this point, the operation should be withdrawn in a timely manner to repair the severely leaking recirculation door and maintain its good rigor. In addition, when starting the feed pump, when the pump is operating normally, the recirculation door should be closed in time to reduce the power loss at this time.
4 application of variable frequency controller
Pump frequency conversion speed regulation operation refers to that the water pump runs under the speed-adjustable motor drive, and the operating point of the pump device is changed by changing the rotation speed. This greatly expands the effective working range of the pump and is a very important and applicable adjustment method in the project. At present, the electrical energy consumed by the motor accounts for about 65% of the industrial power consumption. The vast majority of the equipment used is still a general non-motorized motor. If these non-speed-regulating motors are converted to speed-regulating motors, and their power consumption changes with the load, a large amount of electric energy can be saved. According to the principle of centrifugal pump, the flow rate, head and power of the pump are proportional to the primary, secondary, and tertiary powers of the rotational speed, respectively, under similar conditions. For occasions in which water is often changing, the use of variable frequency speed-controlled water pump water supply can significantly reduce throttling losses and have significant energy-saving effects.
High-pressure cleaner application industry
(1) Petrochemical industry
Heat exchanger tube cleaning;
U-shaped tube cleaning;
Floating head heat exchanger shell side cleaning, air cooler fin tube cleaning;
The inner wall of the reactor, the tower tank, and the internal parts of the equipment are cleaned;
Large-scale storage tank surface and inner wall cleaning treatment
(2) Power industry
Remove dirt on the surface or inside of the condenser (box);
Large steam turbine rotors, partitions, and fouling in the shell;
Damaged refractory materials in the furnace and various types of preheating, condenser and other scales can be removed smoothly without damaging the performance of the original equipment;
(3) Aerospace industry
Civil and military aviation airport runway and guardrail cleaning, runway degumming, removal of oil on the apron and traffic markings on the runway, etc.;
Runway cleaning of aircraft carrier platform;
(4) Shipbuilding industry
Since the surface of the hull needs to be sprayed and sprayed regularly, the use of ultra-high pressure water cleaning equipment can easily remove the dirt and surface paint in preparation for repainting;
(5) Automobile manufacturing industry
Paint and dirt cleaning in automobile painting workshop;
(6) Construction and bridge industry
Building exterior wall cleaning;
Strip the old coating on the wall of the building;
Peel off the hard synthetic fiber coating on the ground;
Bridge maintenance, rust removal and anticorrosion;
(7) Municipal engineering
Chewing gum cleaning on urban streets;
Zebra crossing cleaning on urban roads;
Urban graffiti cleaning;
Urban psoriasis cleaning;
City gas pipeline cleaning.
Hot Water Pressure Washer,Hot Power Washer,Hot Pressure Washer Machine,High Pressure Washer Cleaner
Ningbo Senmiao Trading Co., Ltd. , https://www.senmiaowasher.com