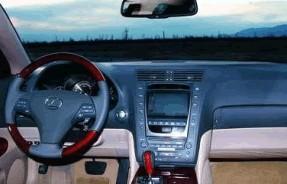
The average amount of plastics used in China's economy cars is about 50 kilograms, which is far below 130-180 kilograms per car in developed markets such as the United States.
This means that Chinese cars use more metal, cars are heavier, fuel efficiency is lower, and there may be more pollution.
Some domestic and foreign auto industry officials believe that the Chinese auto industry is ready to rapidly adopt more plastic technologies as part of a broader strategy for the industry to become more environmentally friendly.
They have taken a substantial step: a group of multinational plastic suppliers and Chinese car companies announced on November 28 that they have established a technology alliance to increase the use of plastics in the Chinese automotive industry. The participating multinational resin suppliers include Rhodia, DSM and Arkema. Automobile manufacturing companies include Changan Automobile Group, Geely Holding Group and Beiqi Foton Motor Co., Ltd.
The alliance was announced at the 6th International Automotive Lightweight Plastics and Innovative Materials Development Forum held in Luzhou, Hebei, where several Chinese automakers talked about their plans to increase the use of automotive plastics and introduced the current The challenge.
Cao Du, chairman of the International Automotive Lightweight Technology Alliance and vice president of Chang'an Automobile Group Engineering Institute, said that he believes that the Chinese automotive industry will quickly move closer to the developed countries in terms of the amount of plastic used for vehicles.
As of now, Chinese automakers have been working hard to improve quality. However, the pressure from the government and the new demand brought by electric vehicles have all mentioned the importance of car weight reduction, Cao Du said.
Cao Du is also the organizer of the summit and the Vice Chairman of the Automotive Plastics and Innovative Materials Committee (APIMC) of the China-European Chemical Manufacturers Association headquartered in Shanghai.
An executive at the Chinese automaker Beiqi Foton Motor Co., Ltd. said at the meeting that engineering plastics is playing a more important role in the design of the company, but he urged the industry to reduce the price of this part of the plastic, which is conducive to better Popularity.
Gao Yan, Vice President of the Automobile Engineering Research Institute of Beiqi Foton and a copy of the procurement department, said: “We have been working on the lightweighting of automobiles for the past few years. Engineering plastics is our direction, and we hope to replace metal with plastic parts. Other aluminum alloy parts. The resulting weight loss is obvious."
For example, he said that Beiqi Foton has changed the bumpers of its medium- and heavy-duty trucks from steel to plastic materials, and has activated glass-reinforced plastic in some auto parts, and has also replaced some steel engine parts with plastic parts.
Gao Yan said that consumers' attitudes are changing. In the past, truck buyers preferred heavy trucks that used large amounts of steel because they appeared to be better able to handle heavy loads, but as the government vigorously promoted resource conservation, customers were encouraged to accept lighter but equally strong new materials.
A speaker from Dongfeng Motor Co., a Wuhan-based company, said that the use of engineering plastics in vehicles in China "still has a huge space." He said that Dongfeng Motor is adopting advanced technologies such as microcellular foam molding and sees the important value of plastic in the application of weight reduction for automobiles.
Yang Dan, head of automotive materials at the company, said: “In the past we have been using foreign innovations. In the future, we hope to be able to independently innovate and develop our own materials and processes.â€
Liu Qiang, director of material engineering at the Geely Automobile Research Institute, said that Geely is applying plastics more to bumpers, front-end modules, windows, and other components, while also trying to use plastics and fiber composites.
Liu Qiang said: "We have incorporated these products into the design of new vehicles. The overall vision has been formed and will incorporate lightweight technologies."
Some Chinese companies are developing more advanced technologies, such as Tier One automotive supplier Ningbo Huaxiang Group Co., Ltd., which is currently developing high-pressure resin transfer molding technology and trying to mass-produce carbon fiber composite materials in an economical manner. Automotive structural parts.
Karsten Brast, general manager of Ningbo Huaxiang Auto Parts R&D Co., Ltd. and former manager of automotive parts supply in Europe, said: “When it comes to [replacement] components, we must mention Carbon fiber composite material."
He said that in Germany, the average steel structure of each vehicle is about 60%, but most of them can be replaced with lightweight materials.
Although Chinese auto companies are eager to replace steel parts with plastics, they have not taken new actions quickly to adopt new technologies such as gas-assisted injection molding to reduce the weight of existing plastic parts and specialize in the production of microcellular foam molding systems. Tang Qinghua, director of the Processing Technology Institute of Beijing Zhongtuo Machinery Co., Ltd., said.
Many speakers said that the Chinese auto industry needs to establish a new business model, cost-effectively conduct R&D and sharing, and help them to innovate more. Many speakers also said that they hope to greatly improve the supply chain. The cooperation of the links.
However, the study of lightweight technologies may take several years to complete, and it is impractical to allow only one area of ​​the supply chain to bear R&D risks. The automotive business of the company’s headquartered in Lyon, France, is the automotive supplier of Rhodia. Jean-Claude Steinmetz, vice president, said.
At the same time, Steinmetz, who is also chairman of APICM, the organizer of the conference, said that the status of China’s auto industry is increasingly important and will play a greater role in global development.
He asked the participants: “Everyone here will be the leader in the automotive industry, and the Chinese auto industry will have different channels for R&D financing. You are ready to adapt to this model and ensure that you can work together to provide these projects. Capital?"
Even if plastics and automotive engineers can solve these problems, they still face a big obstacle: As consumers like larger, more fully equipped cars, cars have become more and more heavy in the past 30 years.
Taking the VW Golf model as an example, the weight of the car in 1974 was about 750 kilograms, but today's golf car has a weight of 1270 kilograms and shows a further growth trend, Carsten said in a speech.
He said that this trend needs to be reversed, especially the heavy-duty batteries used in electric vehicles will further increase the weight of the vehicle.
Machining Steel is the use of CNC machining out,and the machining services including drilling, boring, cutting,meatl bending/metal bending, machining Steel Product material: carbon steel, 20#, 45#, A3, Q235,35Cr2MnMo and other series. In the high-speed machining out of the workpiece has a good finish. But machining Steel of the workpiece is easy to rust, so it will do heat treatment, surface nickel plating, chromium plating, surface black heat treatment, etc.. We have a special inspection department to carry out inspection, ensure the material aging hardness and each size to meet the requirements of the drawings, including the machining steel parts application in various industries: automotive, marine, communications, medical equipment, industrial automation equipment.Except them,we supply the sheet metal operations.
Machining Steel, CNC Machining Steel, Machining Steel Parts, Metal Machining
Hong Kong RYH CO., LTD , https://www.szcncturning.com