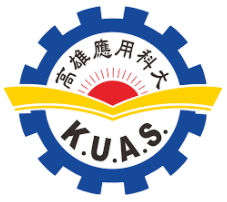
- Customer: Kaohsiung University of Applied Sciences
- Region: Taiwan
- Industry: Research & Education
- Solution:  Moldex3D Advanced / Powder Injection Molding Module / Multi-component Molding Module
- View PDF Version
Executive Summary
Powder injection molding (PIM) is commonly used in manufacturing complicated parts such as this one-piece zirconia dental implant (Fig. 1). Â However, undesirable warpage and shrinkage issues occurred during the two-shot injection molding process. This case focuses on optimizing process parameters through the Taguchi method to improve warpage, reduce shrinkage and achieve uniform powder concentration. Â Moldex3D Filling, Packing and Warp analyses were also carried out to evaluate the effects of different process parameters on part quality.
Fig. 1Â The one-piece zirconia dental implant, including the first shot (left) and second shot (right)
Challenges
- Dimensional variation problem
- Non-uniform powder concentration
Solutions
Using Moldex3D Powder Injection Molding and Multi-component Molding (MCM) modules to predict potential molding problems and use the Taguchi method to find the best possible process parameters to improve part quality.
Benefits
- Minimized warpage and achieved uniform powder concentration
- The part quality of the first shot has been improved by 12.12%; the quality of the second shot has been improved by 59.03%
- Reduced mold reworks and costs
- Successfully shortened product development time
Case Study
The main objective of this case is to improve non-uniform shrinkage and powder concentration in the green parts. In order to solve this problem, the KUAS team utilized Moldex3D to identify the best possible process conditions of the Multi-component Molding (MCM) process.
Firstly, the KUAS team used Moldex3D Powder Injection Molding module to analyze the original design. The simulation results showed that the non-uniform shrinkage would cause significant warpage in the two-shot molding green parts and could lead to decrease in structure strength.
The Taguchi method was used to decide the process parameters such as filling time, packing pressure, mold temperature and melt temperature. The orthogonal array of the Taguchi method suggested 4 different parameters with three levels, and the KUAS team optimized the parameters of manufacturing the one-piece zirconia dental implant. As a result, the warpage of both shots was minimized. The first-shot warpage was reduced from 0.488 mm to 0.145 mm, and the second-shot warpage was reduced from 0.059 mm to 0.022 mm (Fig. 2 & Fig. 3). The powder concentration also became more uniform (Fig. 4 & Fig. 5). It enabled them to produce higher quality parts without making additional mold changes.
Fig. 2Â Total warpage displacement analysis results of the first shot (left) and the second shot
(right) of the original design
Fig. 3Â Total warpage displacement analysis results of the first shot (left) and the second shot
(right) of the optimized design
Fig. 4Â The powder concentration results of the first shot (left) and the second shot
(right) of the original design
Fig. 5Â The powder concentration results of the first shot (left) and the second shot
(right) of the optimized design
Results
With Moldex3D analysis, KUAS was able to improve dimensional,warpage, and powder concentration issues prior to actual production (Table 1). Through the Taguchi method, the part quality of the first shot has been enhanced by 12.12%; the quality of the second shot has been enhanced 59.03%. In addition, Moldex3D allows users to improve non-uniform powder concentration prior to actual production and further enhance the product quality, saving costs on mold trials and shorten time-to-market.
The First Shot
 | Warpage (mm) | Powder Concentration (%) |
Original Parameters | 0.165~0.002 | STD 1.089 |
Optimal Parameters (Taguchi method) | 0.145~0.002 | STD 6.1 E-5 |
The Second Shot
 | Warpage (mm) | Powder Concentration (%) |
Original Parameters | 0.0454~0.0001 | 4.941 |
Optimal Parameters (Taguchi method) | 0.0186~0.0004 | STD 4.2E-4 |
Table 1 Comparison between the effects of original and optimal parameters on part quality
Sight Glass ,level gauge, sight tube,Refrigeration System Sight Glass
SUZHOU YOUDE ELECTRIC CO., LTD. , https://www.unitekool.com