First, visual inspection Visual inspection is one of the important methods of non-destructive testing. It refers only to a method of detecting or measuring the surface of an industrial product with the human eye or with the aid of an optical instrument. Typically, visual inspection is limited to the visible range of the electromagnetic spectrum.
Visual inspection can be divided into direct visual inspection and indirect visual inspection. Direct visual inspection means that the test piece is directly detected with the human eye or with a magnifying glass having a magnification of 6 times or less. Indirect visual inspection refers to the direct observation of areas that cannot be directly observed using various optical instruments or equipment, such as the use of mirrors, telescopes, industrial endoscopes, fiber optics, or other suitable instruments for detection.
Second, endoscope detection There are many kinds of visual inspection instruments, and industrial endoscopes are one of them. The earliest detection of endoscopes was used for medical examinations of the human body. In the 1950s, it began to enter the field of industrial inspections, and specialized industrial endoscopes appeared. Domestic introduction of industrial endoscope products from abroad in the 70s to 80s of the 20th century was mainly used for the control of excess internals in aerospace products and the quality inspection of some components. In recent years, domestic endoscope detection has entered a practical stage, more and more used in the control of product quality, and developed into a dedicated detection method.
Endoscopy is a detection technology that has been widely used in recent years with the development of endoscopic manufacturing technology. Endoscope detection requires the use of an industrial endoscope (abbreviated as an endoscope) as a detection tool, and an industrial endoscope is specially designed and manufactured to meet the requirements of industrial complex use environments. According to the characteristics of the manufacturing process, we usually divide the endoscope into three types: straight mirror, fiberscope, and video mirror. The comparison of the three types of performance is shown in Table 1: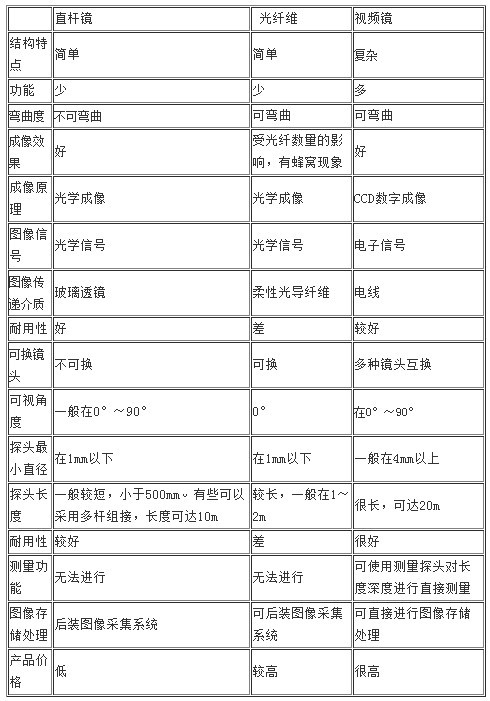
Third, there are many types of endoscopes used for endoscopes, and different types of endoscopes have different application ranges. In addition to considering the type of endoscope, in the specific selection also need to consider the probe diameter, length, visual direction, focal length and other technical indicators, and due to the endoscope's use of the environment is complex, need to consider its waterproof, oil, and resistance Corrosion, wear and other properties. Generally, the type of endoscope to be used is determined according to the location and requirements of the specific test object, and at least the position, direction, minimum resolution requirement, path, measurement record, etc. of the test should be considered. Complex products often require the use of multiple models. In general, we believe that: rod mirror is easy to use, durable, good imaging effect, used for products that do not need to bend, detection range is within 500mm, suitable for the detection of straight holes. The video mirror has many functions, flexible use, high reliability and wide applicability. It is suitable for a variety of products with complex internal structures or occasions where quantitative detection and contrast analysis are required. However, due to the manufacturing technology, the CCD chip on the probe is impossible. Made very small, so that the probe diameter is difficult to less than 4mm. Video mirrors can be used instead of straight mirrors and fiber optics. Fiberoptic mirrors are easily damaged, have a short service life, and have poor sharpness. Imaging effects and bending performance are far inferior to those of videoscopes, but their diameters can be made very thin. They are mostly used for products with an internal diameter of 4mm or less that cannot be detected by videoscopes.
Fourth, the main factors affecting endoscopy detection The main factors affecting endoscopy detection are:
1. Lighting conditions. Most endoscopes use an endoscope with its own light source for illumination. Under normal conditions, the color temperature of endoscope detection lighting source is not lower than 5600K, and the illumination intensity is not lower than 2600lm.
2. Probe position and angle. It is usually best to observe the image in the range of 5~25mm from the detection area. Therefore, the endoscope probe is often required to be close to the observation point. A good observation effect can be achieved within the range of 45 ゚~90 探头 between the probe and the observation object plane. In practice, the optimal observation position is obtained by repeatedly changing the position and angle of the probe and the observation point, and the best detection is obtained. effect.
3. Channel. Select the channel should be close to the need to detect the location, choose to enter the shortest length of the channel, to minimize the number of probes need to bend and degree; first consider the top to bottom, from high to low channel; preferred wide channel; recommended tooling , to ensure the correct direction of the probe in the product channel; should be used to observe the edge of the way through the channel.
4. The distortion of the image. Observed by the lens deformation phenomenon of the object, with the distance from the lens center to the edge of the image distortion occurs. The distortion of the image will affect the judgment and measurement of defects. The distortion of the image is large when viewed by a rod mirror or a fiberscope, and the video endoscope can be corrected by a computer.
5. Resolution, magnification, detectable minimum defects. These are the technical indicators of the endoscope itself and can directly affect the detection results.
6. The surface reflectivity of the object. Different surfaces have different reflectivity, and are related to the material's material and surface roughness. Therefore, the actual intensity of the endoscope illumination should be selected according to the actual situation in order to obtain clear and useful results.
V. Application in the endoscope industry The inspection scope of the industrial endoscope is given in QJ2859-1996 "Industrial Endoscope Operation Methods and Decision Rules":
(1) Inspect the lumen. Check for defects such as surface cracks, peels, pull lines, scratches, pits, bulges, spots, and corrosion.
(2) Weld surface defect inspection. Check the weld surface cracks, incomplete penetration, and weld leakage.
(3) Assembly inspection. When there are requirements and requirements, use the endoscope to inspect the assembly quality; after the assembly or a certain process is completed, check whether the assembly positions of the zero and the parts are in accordance with the requirements of the drawings or technical conditions; if there are assembly defects.
(4) Status check. When some products (such as worm gear pumps, engines, etc.) work, endoscopy is performed according to the items specified in the technical requirements.
(5) Check for unwanted items. Inspect the product for residual debris, foreign objects, etc.
(6) Size measurement. For measurements that require measurement, measurement probes can be used.
Six, endoscopy and determination rules (1) crack. When the light beam hits the surface of the object to be detected, black or bright lines are observed, and if the lines have irregular edges under a certain magnification, it is determined as a crack. When the crack is wide, the measured influence line of the measurable probe bends.
(2) from the skin. When the beam is irradiated in parallel, a shadow is observed behind the convex portion; changing the beam irradiation angle, it is observed that there is a clear demarcation line between the convex portion of the surface and the surrounding object to be detected, and it is determined as a peeling.
(3) Pull and scratches. Under the light beam irradiation, it was observed that there was a regular continuous long line on the surface, and it was determined as a pull line.
(4) Pits are raised. When the light beam is irradiated at a certain angle, it is connected with the boundary of the surrounding objects and there is no dividing line. The part near the light source has a shadow, and the light source far from the light source has a shadow, which is a pit. When the light beam is irradiated at a certain angle, it is connected with the boundary of the surrounding objects and there is no dividing line. The raised part has bright shadows, and the back shadows are pits. When the pit is deep or raised, the measuring line of the measurable probe bends.
(5) Spots. When the light beam is irradiated, a smooth and non-convex surface that is different in color from surrounding objects is observed as a spot.
(6) Corrosion. Under the irradiation of light beam, a blocky, spot-like non-smooth surface was observed, and under a certain magnification, slight unevenness was caused by corrosion.
(7) Incomplete penetration. Obvious demarcation lines between the molten metal and the base metal and the weld seam were observed.
(8) Solder leakage. When the light beam is irradiated at a certain angle, it is observed that the molten metal is connected to the molten metal. When there is no ridge of the dividing line, the solder leakage occurs.
(9) excess material. When the light beam is irradiated at an arbitrary angle, objects other than the structure having a difference in the color and brightness of the surrounding basic sample become redundant.
(10) Assembly defects. At the time of testing, structural phenomena that did not meet the technical conditions of the pattern were observed.
(11) Measurement of dimensions. The measurement probe can be used to measure the size of the shape when required.
VII. The situation of foreign visual inspection standards The research and formulation of visual inspection technology and related standards have been carried out comprehensively in foreign countries, and their applications have also been extensive. Especially in developed countries such as Europe and the United States, research and development of visual inspection standards have reached a high level. Currently, the ASME standards in the United States, the RCC-M standards in France, and the BSEN standards in the United Kingdom all have the specific content of visual inspection methods and form a different standardization system.
Visual inspection can be divided into direct visual inspection and indirect visual inspection. Direct visual inspection means that the test piece is directly detected with the human eye or with a magnifying glass having a magnification of 6 times or less. Indirect visual inspection refers to the direct observation of areas that cannot be directly observed using various optical instruments or equipment, such as the use of mirrors, telescopes, industrial endoscopes, fiber optics, or other suitable instruments for detection.
Second, endoscope detection There are many kinds of visual inspection instruments, and industrial endoscopes are one of them. The earliest detection of endoscopes was used for medical examinations of the human body. In the 1950s, it began to enter the field of industrial inspections, and specialized industrial endoscopes appeared. Domestic introduction of industrial endoscope products from abroad in the 70s to 80s of the 20th century was mainly used for the control of excess internals in aerospace products and the quality inspection of some components. In recent years, domestic endoscope detection has entered a practical stage, more and more used in the control of product quality, and developed into a dedicated detection method.
Endoscopy is a detection technology that has been widely used in recent years with the development of endoscopic manufacturing technology. Endoscope detection requires the use of an industrial endoscope (abbreviated as an endoscope) as a detection tool, and an industrial endoscope is specially designed and manufactured to meet the requirements of industrial complex use environments. According to the characteristics of the manufacturing process, we usually divide the endoscope into three types: straight mirror, fiberscope, and video mirror. The comparison of the three types of performance is shown in Table 1:
Table 1: Comparison of three types of endoscope performance
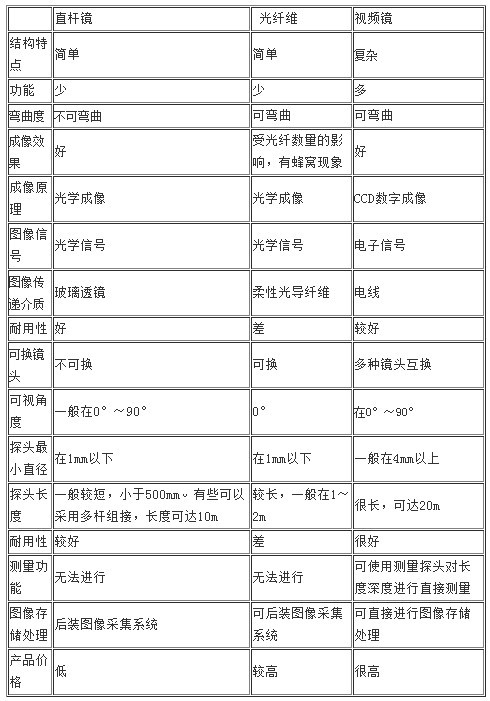
Fourth, the main factors affecting endoscopy detection The main factors affecting endoscopy detection are:
1. Lighting conditions. Most endoscopes use an endoscope with its own light source for illumination. Under normal conditions, the color temperature of endoscope detection lighting source is not lower than 5600K, and the illumination intensity is not lower than 2600lm.
2. Probe position and angle. It is usually best to observe the image in the range of 5~25mm from the detection area. Therefore, the endoscope probe is often required to be close to the observation point. A good observation effect can be achieved within the range of 45 ゚~90 探头 between the probe and the observation object plane. In practice, the optimal observation position is obtained by repeatedly changing the position and angle of the probe and the observation point, and the best detection is obtained. effect.
3. Channel. Select the channel should be close to the need to detect the location, choose to enter the shortest length of the channel, to minimize the number of probes need to bend and degree; first consider the top to bottom, from high to low channel; preferred wide channel; recommended tooling , to ensure the correct direction of the probe in the product channel; should be used to observe the edge of the way through the channel.
4. The distortion of the image. Observed by the lens deformation phenomenon of the object, with the distance from the lens center to the edge of the image distortion occurs. The distortion of the image will affect the judgment and measurement of defects. The distortion of the image is large when viewed by a rod mirror or a fiberscope, and the video endoscope can be corrected by a computer.
5. Resolution, magnification, detectable minimum defects. These are the technical indicators of the endoscope itself and can directly affect the detection results.
6. The surface reflectivity of the object. Different surfaces have different reflectivity, and are related to the material's material and surface roughness. Therefore, the actual intensity of the endoscope illumination should be selected according to the actual situation in order to obtain clear and useful results.
V. Application in the endoscope industry The inspection scope of the industrial endoscope is given in QJ2859-1996 "Industrial Endoscope Operation Methods and Decision Rules":
(1) Inspect the lumen. Check for defects such as surface cracks, peels, pull lines, scratches, pits, bulges, spots, and corrosion.
(2) Weld surface defect inspection. Check the weld surface cracks, incomplete penetration, and weld leakage.
(3) Assembly inspection. When there are requirements and requirements, use the endoscope to inspect the assembly quality; after the assembly or a certain process is completed, check whether the assembly positions of the zero and the parts are in accordance with the requirements of the drawings or technical conditions; if there are assembly defects.
(4) Status check. When some products (such as worm gear pumps, engines, etc.) work, endoscopy is performed according to the items specified in the technical requirements.
(5) Check for unwanted items. Inspect the product for residual debris, foreign objects, etc.
(6) Size measurement. For measurements that require measurement, measurement probes can be used.
Six, endoscopy and determination rules (1) crack. When the light beam hits the surface of the object to be detected, black or bright lines are observed, and if the lines have irregular edges under a certain magnification, it is determined as a crack. When the crack is wide, the measured influence line of the measurable probe bends.
(2) from the skin. When the beam is irradiated in parallel, a shadow is observed behind the convex portion; changing the beam irradiation angle, it is observed that there is a clear demarcation line between the convex portion of the surface and the surrounding object to be detected, and it is determined as a peeling.
(3) Pull and scratches. Under the light beam irradiation, it was observed that there was a regular continuous long line on the surface, and it was determined as a pull line.
(4) Pits are raised. When the light beam is irradiated at a certain angle, it is connected with the boundary of the surrounding objects and there is no dividing line. The part near the light source has a shadow, and the light source far from the light source has a shadow, which is a pit. When the light beam is irradiated at a certain angle, it is connected with the boundary of the surrounding objects and there is no dividing line. The raised part has bright shadows, and the back shadows are pits. When the pit is deep or raised, the measuring line of the measurable probe bends.
(5) Spots. When the light beam is irradiated, a smooth and non-convex surface that is different in color from surrounding objects is observed as a spot.
(6) Corrosion. Under the irradiation of light beam, a blocky, spot-like non-smooth surface was observed, and under a certain magnification, slight unevenness was caused by corrosion.
(7) Incomplete penetration. Obvious demarcation lines between the molten metal and the base metal and the weld seam were observed.
(8) Solder leakage. When the light beam is irradiated at a certain angle, it is observed that the molten metal is connected to the molten metal. When there is no ridge of the dividing line, the solder leakage occurs.
(9) excess material. When the light beam is irradiated at an arbitrary angle, objects other than the structure having a difference in the color and brightness of the surrounding basic sample become redundant.
(10) Assembly defects. At the time of testing, structural phenomena that did not meet the technical conditions of the pattern were observed.
(11) Measurement of dimensions. The measurement probe can be used to measure the size of the shape when required.
VII. The situation of foreign visual inspection standards The research and formulation of visual inspection technology and related standards have been carried out comprehensively in foreign countries, and their applications have also been extensive. Especially in developed countries such as Europe and the United States, research and development of visual inspection standards have reached a high level. Currently, the ASME standards in the United States, the RCC-M standards in France, and the BSEN standards in the United Kingdom all have the specific content of visual inspection methods and form a different standardization system.
Sun Visor,Car Sun Shade,Sun Visor Car,Car Visor
Ningbo Yonghai Auto Products Co., Ltd. , https://www.yonghai-manufacturer.com