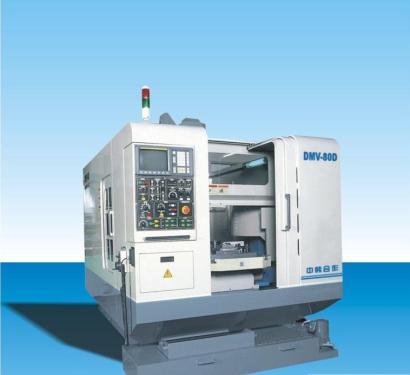
As a "machine manufacturing machine", after more than ten years of development, China's machine tool industry has become the largest importer and consumer nation for eight consecutive years. “Although China is currently a big machine tool manufacturing country, there is a tendency for the manufacturing process to be biased towards a low end,†said Luo Baihui, chief analyst of Jinmo Machine Tool Network.
According to the data released by the China Machine Tool Industry Association, all rights reserved in 2011, the growth rate of China's imports of machine tool products remains high, with a total import value of US$ 20.29 billion and exports of US$ 8.90 billion.
In 2010, the trade deficit of China's machine tools was only US$8.042 billion. By 2011, the trade deficit of China's machine tool industry was as high as US$11.39 billion, and the number of imports that grew year by year increased unabated. Luo Baihui believes that the main reason for this gap is that, on the one hand, in recent years, the explosive growth in the demand and supply of ordinary machine tools in China has constrained the overall technological level of users, and has also slowed down the overall manufacturing level of the machine tool industry. On the other hand, the lack of independent innovation capability of domestic enterprises can not meet the demand for products with high technical requirements such as heavy-duty machine sheets, which is also a structural problem in China's machine tool products.
The core technology of the machine tool is a numerical control system. At present, not to mention the system, even the slightly better CNC machine tools made in China, the high-precision ball screws used, and the bearings are mainly imported from Japan. China's self-produced ball screw has bearing problems in accuracy and life. Domestic major machine tool factories, CNC system 100% purchased.
In the machine tool industry, CNC machines are based on the number of axes, 3-axis and 5-axis are medium-to-high-end products, and 5-axis and higher are high-end products. At present, China's machine tools are mostly low-end products with 3 axes or less. As for why there are many low-end products in China, Luo Baihui said that China's machine tool manufacturing started relatively late, and shortages of professionals and other shortcomings could not be remedied in a short time. To weaken dependence on imports, we should vigorously introduce and cultivate talents and increase investment in R&D of machine tools is the solution. Whether domestic machine tools can break through the siege of imported machine tools, but also whether China's high-end machine tool manufacturing can reach the world's leading level in the future.
Wire Cut EDM is fast, effective, and can be used to machining virtually any electrically conductive metal material, including Bronze, Copper, Tungsten, Carbon graphite, Carbon steel, Stainless steel, High alloy steel, Hard alloy, Inconel, Kovar, Titanium and many others. Computer-automated CNC equipment and advanced CAD/CAM programming guarantee our Wire Cut EDM to meet even the tightest tolerances.
Multiple Cutting Wire Cut EDM,Middle Speed Wire Cut EDM,CNC Wire Cutting EDM Machine,High Precision WEDM
Jiangsu Sailing Intelligent Equipment Co., Ltd. , https://www.sailingcnc.com