After sales exceeded 40,000 units in 2010 and the country’s total capacity reached 120,000, Beiqi Heavy was facing new challenges. As the service spare parts system is still relatively weak, the Beiben service system is difficult to keep up with the rapid growth of sales, and it may delay the company's 12th five-year strategy. As a result, in 2011, Beiben Heavy Industries put its focus on the entire changers and capacity enhancement.
In the heavy-duty truck industry, there has been a saying: "In a new market, if you can sell two cars, the first one may be sold by sales personnel, but the second one should be sold by after-sales service personnel. "For Beiben, this sentence has a deeper meaning. Wang Shihong, General Manager of Beitou Heavy-duty Truck in Baotou, admitted frankly. “In the past, Beiben heavy trucks had very little sales, and we spent more on sales accordingly. Now, Beiben heavy trucks have reached a certain amount of market share. It is time for us to fully strengthen our services.â€
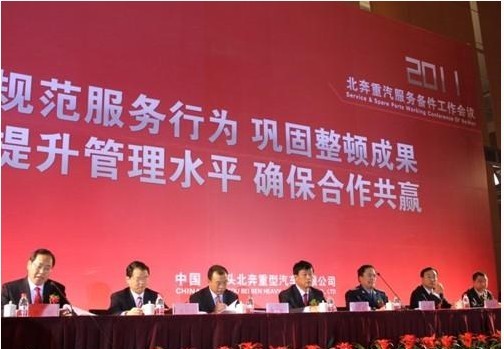
In the past five years, the implementation of Beiben Heavy Duty's service strategy has achieved certain results. On the one hand, the company has initially established an after-sales network covering the entire country with a service radius of less than 100 kilometers. The spare parts network model has also transformed from the former branch company central library to the spare parts regional distribution center agency model, and the spare parts marketization has taken a substantial step; On the one hand, the market support capability of Beiben service spare parts network has been significantly improved. The spare parts reserve of the channel has been increased to 100 million yuan in 2010, and spare parts sales volume has exceeded 240 million, an increase of 33.3% compared with 2009.
In addition, the Beiben 400/800 call center was formally launched on January 1, 2011, and Beijing Beiqi's response to services has taken a big step forward. At the same time, the office building carrying the Beiben Heavy Truck National Spare Parts Distribution Center and Service Center, the 9,000-square-meter spare parts storage center and the old parts management center have also been put into use. "This is not only the improvement and enhancement of hardware infrastructure such as office buildings and storage conditions, but more importantly, it is seeking to improve and upgrade the comprehensive, systematic and professional service spare parts management and control system."
However, with the significant increase in the sales volume of the Beiben heavy trucks in 2010, the total reserve of spare parts and terminal reserves, lagging behind the growth of sales volume and the speed of market development, have become increasingly serious. Moreover, with the development of new markets, the overall strength of service spare parts suppliers and the unbalanced regional development are also becoming increasingly prominent. Wang Baoying, assistant general manager of Beiben Heavy Truck, analyzed that the root of these problems should be attributed to the management problems of Beiben's service spare parts system. Beiping’s management tools are still lagging behind, and some institutions, methods and processes do not meet management needs.
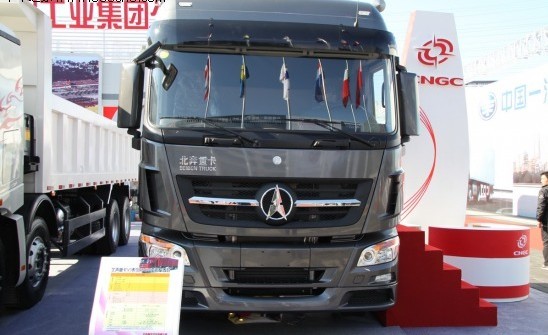
Obviously, how to solve these problems will be the top priority for Beiben Heavy Trucks' service and spare parts work in 2011. At the Beiben Heavy Duty Truck Service Spare Parts Conference in 2011, upgrading and mobilization became the main theme of the company throughout the year. In 2011, the general idea of ​​Beiben heavy-duty truck service spare parts work was to adhere to the concept of careful service, keep abreast of market changes, continuously improve service, promote the rapid development of Beipong, and actively promote the construction and optimization of service networks. , service providers, distribution centers, and business relationships in close cooperation, improve the service management level, operating efficiency, and operation quality of service spare parts systems, and support market development and sales growth.
Under the guidance of this policy, Beiben will fully implement the results of service consolidation achieved in the second half of 2010 in 2011. It is understood that in the second half of 2010, Beiben carried out to increase speed, capacity, parts identification and vehicle files, handheld control, GPS monitoring system, operation of call center, return of old parts, storage, and claims; , process improvement and staffing and enrichment are the main contents, and services for the purpose of improving service quality, service efficiency, service image, and service cost reduction are being reorganized.
This reorganization was personally led by Wang Shihong, the general manager, which lasted more than six months. It has already achieved the phased goal so far and is marked by the establishment of the Beiben Service Center under the control of the sales company. Beiben's improved service management and control system, including management and control procedures, control measures, and management and control standards, will be fully implemented in 2011. At this annual meeting of service and spare parts, seven major measures for the rectification of Beiben's service spare parts system were carefully deployed and mobilized. Among these seven important measures, there are detailed provisions for service center functions, old parts audit management, service policies, spare parts reserves, distribution terminals, and service station maintenance quality.
If, say, the sales growth and market development of Beiben a few years ago are still struggling to drive the development of the service spare parts market and service spare parts seriously restrict the sales situation, then, with the Beilun heavy truck market holding more than 120,000 units in 2011, each year, More than 3 billion service spare parts market has formed a scale, and the market has already formed the power to promote and promote its development, and sales and service spare parts will promote the development of the situation.
Hydraulic Pipe Bending Machine
CTK-NC series single-head high-speed hydraulic Pipe Bending Machine is a product developed by our factory on the basis of absorbing advanced technology at home and abroad. The product is hydraulic transmission, PLC control, and man-machine dialogue operation using touch screen. The whole machine has the advantages of convenient operation, stable performance and high production efficiency. It is an ideal equipment for the pipe fittings processing industry, especially the stainless steel pipe fittings processing industry.
Hydraulic Pipe Bending Machine,Hydraulic Pipe Bender,Hydraulic Tubing Bender,Air Hydraulic Pipe Bender
GUANGDONG CHITTAK INTELLIGENT EQUIPMENT CO.,LTD , https://www.ctkcutting.com