Zyzhan guide: As an important equipment in the pharmaceutical industry, granulators have been continuously developed and innovated. The granulation mechanism has fast particle size and good effect. The special filter screen is designed and carefully sieved. The friction filter rod can crush the sieved solid particles and is widely used in the pharmaceutical, chemical and food industries. This machine can replace the swinging pellet machine and is a new generation of pellet equipment.
The granulator is mainly composed of feeding, stirring, granulating, transmission and lubrication systems. The working process is to require the powder with the water content not more than 15%, enter the feeding auger from the hopper, adjust the speed of the stepless speed regulating motor, obtain the appropriate material flow, and then enter the agitator, stir and steam through the stirring rod Mixing and quenching and tempering, if you need to add molasses or grease, it is also added with steam from the mixing drum to adjust the quality. The amount of oil added is generally not more than 3%, otherwise it is difficult to form. After quenching and tempering, the temperature of the powder can reach 64-85 °C. The humidity is 14 to 16%. Then, the iron impurities mixed in the powder are removed through a chute through a selectable iron absorbing device, and finally enter the press chamber for granulation. The main scope of use of the granulator is as follows:
1. The granulator is a rocking action of a rotating drum. The wet powder material can be ground into particles by a wire sieve, and can also be widely used for pulverizing and becoming a ready-made granule.
2. In the case of chemicals, the powder is used as a wet-laid powder, and after drying, it is used to compress the tablet, and it is also possible to pulverize the block which is agglomerated during storage or agglomerated during chemical processing. It is used industrially to treat confectionery and sugar blends and malt milk, and other industries such as ceramics, plastics and the like into shaped pellets.
3. It is not suitable for semi-solid, fluid, slurry or wear.
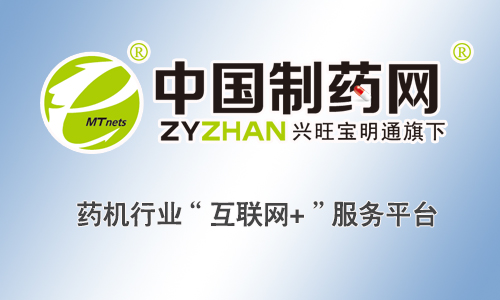
1. The granulator is a rocking action of a rotating drum. The wet powder material can be ground into particles by a wire sieve, and can also be widely used for pulverizing and becoming a ready-made granule.
2. In the case of chemicals, the powder is used as a wet-laid powder, and after drying, it is used to compress the tablet, and it is also possible to pulverize the block which is agglomerated during storage or agglomerated during chemical processing. It is used industrially to treat confectionery and sugar blends and malt milk, and other industries such as ceramics, plastics and the like into shaped pellets.
3. It is not suitable for semi-solid, fluid, slurry or wear.
Henan Aklly Filter Engineering Co., Ltd , https://www.akllyfilter.com